Streamlined Assembly and a Giant Leap in Casting Technology
Tesla has boldly embraced a groundbreaking approach to vehicle design and assembly with its Giga castings. This technology is based on large cast aluminum components produced on presses with clamping forces greater than 6,000 tons. Such components aim at simplifying assembly processes, provide beneficial productivity gains with shorter production time, and a reduction in parts diversity as described in Ducker Carlisle’s white paper from 2022.
This leads to potential changes in future automotive architectures. New EV platforms open the way to increase its utilization of mega-castings due to the lack of design constraints from the absence of a tunnel dedicated to an exhaust system or driveshaft.
Ducker Carlisle has tracked the adoption of mega-castings since its inception. China leads the globe with 0.7M vehicles in 2023 (2.8% of total production) with a mega-casting and is forecasted to grow to over 2M by 2030 (6.4% of total production). NA follows with 0.4M in 2023 (2.4% of total production) while EU lags with just 0.26M (1.8% of total production).
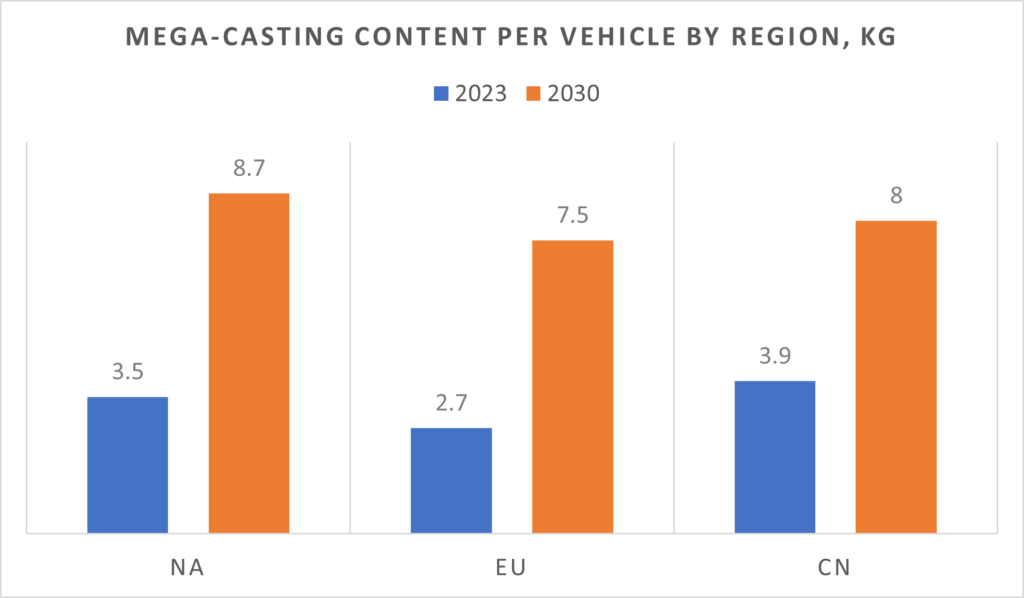
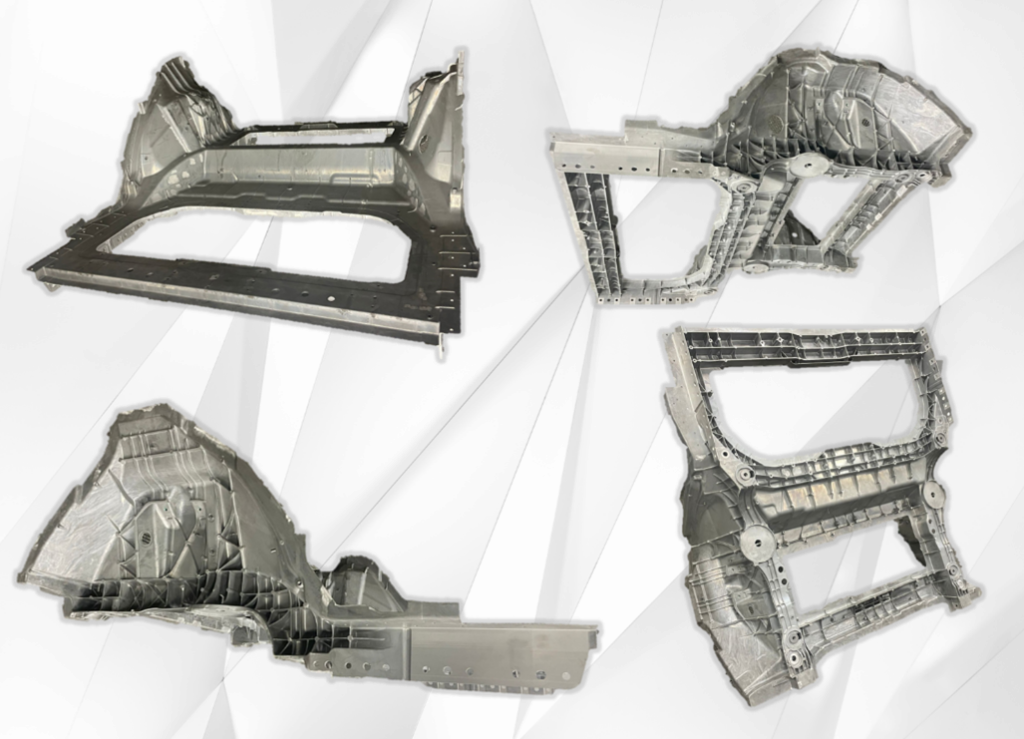
As the production cost of BEVs remain higher than ICE vehicles (mostly due to the battery costs), OEMs must find additional solutions to lower costs and vehicle MSRP, leading to a growing interest for mega-castings. Several Chinese OEMs including HiPhi, NIO, Seres, Xpeng, and Zeekr, have successfully followed Tesla’s steps with mega-casting applications, most of the time outsourced to suppliers such as HongTu, Linamar, TuoPu, and WenCan (Le Bélier). Some OEMs like Li, XiaoMi, HongQi, and ChangAn explore the process and the possibility to develop in-house mega-casting productions. Due to the level of investment, newcomers and new factories are preferred for mega-casting implementation as they tend to bring fewer challenges related to the amortization of existing production lines, lowering the entry point for innovative manufacturing processes.
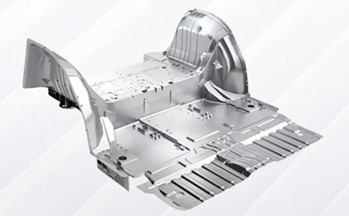
The motivation for the larger adoption of mega-casting in China is the lower cost of large presses (over 6,000 tons), driven by intense competition among local press suppliers such as Yizumi and Haitian. Additionally, Chinese automakers are compelled to showcase innovation by competing with industry giants like Tesla. The adoption of mega-castings serves as a powerful marketing strategy. This combination of factors contributes to the rapid adoption of mega-casting in China while legacy carmakers in the US and the EU still weigh the advantages of moving forward with mega-castings or asking suppliers to make the necessary investments to produce these components.
Investment barriers and technology improvements
There are high investment thresholds for mega-castings. Current technologies require 6,000-ton (and often times larger) presses compared to 4,400-ton machines for the largest legacy (high pressure vacuum die) cast parts. The tooling required for these large presses also add to the barriers of entry including highly specialized mold designs (flow patterns, size, and robustness of the die) and the annual cost to maintain and replace these molds after 100K shots. Although the industry has recorded monumental improvements, the scrap rate remains high (2-digit percentage of rejection rate for components is unseen in the automotive industry). The difficulty to achieve perfect components at first with the potential presence of porosity is enhanced by the lack of heat treatment because of the component size. Heat-treatment helps prevent cracks and secure the integrity of the parts. Currently, OEMs are applying different solutions including ultrasonic inspections or X-rays to identify hidden defects. Improvements include the development of new alloys that don’t require heat-treatment and mitigate the occurrence of porosity-related issues.
There are other solutions being investigated to improve productivity, costs, and quality, including going with larger presses, some exceeding 12,000 tons, and up to 20,000 tons for the largest press announced to date. OEMs and suppliers are exploring additional innovations including new alloys and exploring Rheocasting (semi-molten alloy injection to improve penetration of material in the die) as a viable alternative.
Aging and the lack of return on experience
There is a paradoxical attitude in the automotive industry which opposes the continuous need for innovation and the robustness of solutions based on experience. As a matter of fact, the current lack of return on experience adds to the cost of investment for legacy OEMs’ hesitations. Tesla and Chinese OEMs race for innovation and remain focused mostly on production cost. Legacy OEMs tend to consider more complex business models and approaches including vehicle maintenance, parts, services, and liability as essentials.
The recent introduction of mega-casting prevents from answering questions on durability and the impact of aging. One occurrence of cracks in the mega-casting of a Tesla Model Y has been reported by one owner. No other incident has been reported, and it will take years to define whether this will remain an isolated incident or if it’s the tip of the iceberg. The latter would generate concerns in terms of respect for the vehicle safety and design, particularly related to crashworthiness and energy absorption in case of a major crash. It tends to illustrate and justify the hesitation of carmakers such as Mercedes-Benz who has changed its strategy twice towards mega-castings and particularly where best within the BIW to utilize them.
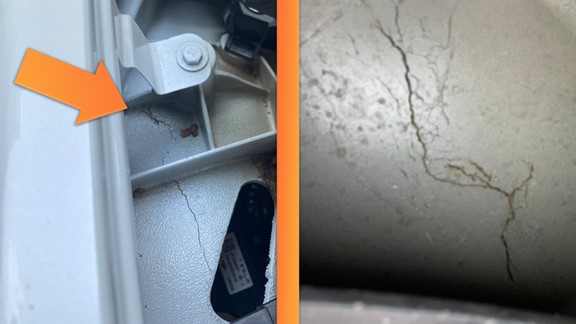
In the meantime, repairability of mega-castings remains a hot topic. On one hand, we can consider it is a secondary focus as an impact dissipating enough energy to break a mega-casting would likely result in significant damage to any vehicle beyond repair (total loss). But the lack of return on experience doesn’t yet provide enough data to cope with such an assumption. On the other hand, replacement of a mega-casting component nearly impossible, while repairability would require redesigning these components and creating new subcomponents (castings and extrusions) with specific repair zones
Opening Pandora’s box
Tesla opened Pandora’s box with its Gigacasting solution. Mega-castings caught the automotive industry’s attention with several carmakers making announcements about their interest in such an architecture. However, few manufacturers have yet publicly committed to the adoption of such technology and the platform architecture necessary to achieve the integration of meg-castings. Manufacturers and equipment suppliers are leveraging return on experience and innovations in aluminum castings to further integrate multiple components into single parts to improve production process without the need for oversized presses. Large castings appear as one possible outcome. These integrate shock towers, longitudinals, and cross members into one component, without the difficulty to add walls, the most difficult area to achieve in mega-castings. Ultimately, large castings can be produced with 4,400-ton presses.
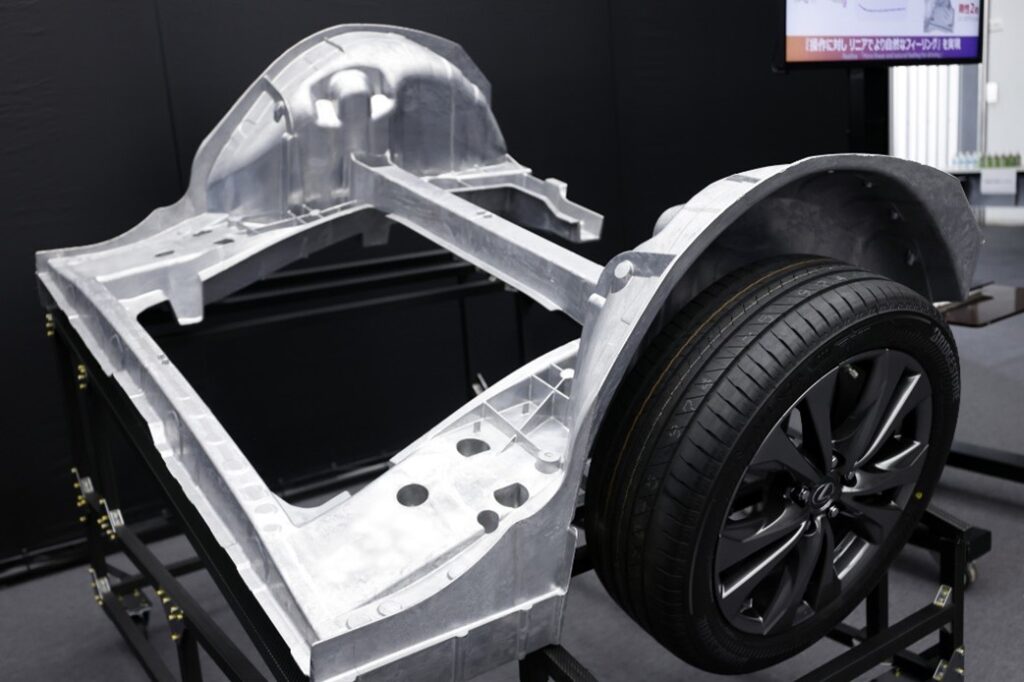
The mega-casting disruption has impacted most carmakers now considering innovation beyond large and mega aluminum casting, including potential for easier assembly of steel, plastics, and composite large modules. Not everyone may adopt mega-castings, but Tesla has shaken the automotive industry and opened the way to innovation in vehicle platforms and manufacturing.
Ducker Carlisle’s decades of automotive consulting experience and comprehensive expertise in auto and light truck manufacturing, electrification, aftersales, and parts benchmarking help automotive clients secure an advantage in a shifting global market. Learn more here.
Article Prepared By:
Bertrand Rakoto, Director – Global Automotive Practice Leader
Leonard Ling, Senior Analyst – Automotive Knowledge Manager