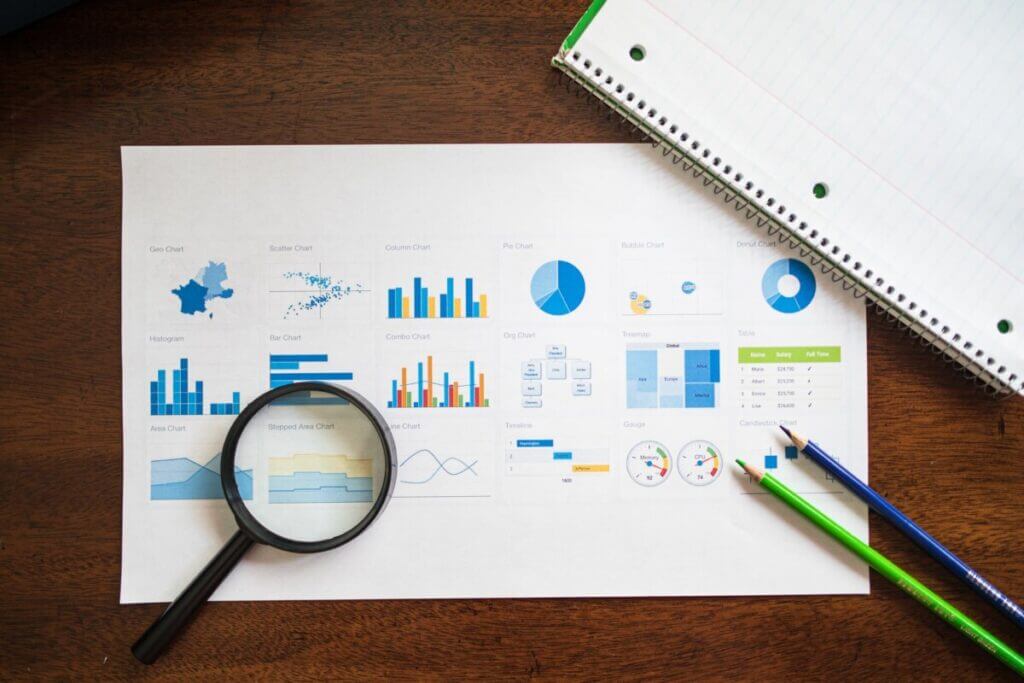
Raw Materials
Two key KPIs to consider for raw materials are the weight of the raw materials and the acreage of the area of manufacturing and extraction. OEMs within the aftersales space may consider monitoring both their own performance in these raw material KPIs and the performance of the various available suppliers. This is especially valuable due to the large portion of parts manufactured outside of the OEMs’ direct influence.
Weight by Raw Material by Type – The weight of each input is needed in order to calculate the efficiency of our processes. Monitoring the location sites and regions for these materials is necessary for understanding the impact to the area. The aftersales industry can track these values via standardized bookkeeping procedures. The amount matters – one ton of material has a bigger environmental impact than half a ton of material. It’s more involved to extract the material, it requires more processing, and it takes more energy to ship. The type of material also matters – one ton of wood has a far different impact than one ton of gold.
Acreage for the Manufacturing & Extraction Plant – This is the physical footprint of a plant, both with regards to the space it occupies for its daily operations, as well as the space it occupies and damages during its raw material extraction processes. The extent to which land is damaged varies from material to material. Monitoring and correcting for this damage provides longevity to the site, and in turn, sustainability for the organization.
Energy & Emissions
The next type of KPIs that we will focus on is related to energy and emissions. The reason we include these together is that energy is the primary driver of emissions. While it’s possible to have emissions without energy use, these situations are rare, and we gain more value from combining the two metrics. As our ultimate goal is to eliminate emissions, limiting energy use, by itself, serves no purpose. Because energy use is easier to measure, more accessible, and more comparable than emissions, we use energy KPIs and then convert these into the emissions KPIs to measure our true impact.
Greenhouse Gas Emissions – The total greenhouse gas emissions (in particular, CO2) is the KPI most often used to measure the carbon footprint of the manufacturing process. Nearly every source mentions this KPI, and we agree – it’s the most important. While the aftersales industry should be aware of the emissions generated during the manufacturing process, the emissions generated from transportation processes are also very important to measure. We measure these emissions in weight of CO2 (or other gases). But it’s hard to come up with a measure without further information.
Kilowatt Hours (kWh) Consumed, by Source – According to the EPA[1], roughly two thirds of industrial emissions are created from energy generation, while the remainder is from various leaks and inefficiencies. It is commonly understood that improving quality control and shipping procedures can reduce energy usage while also driving better returns. Moving goods requires power, which should be measured in kWh. In what’s called “fuel energy”, a conventional truck is over 5 kWh per mile traveled[2]. The less energy used, the lower total emissions will be.
Non-Renewable Resource Consumption for Energy Generation – Non-Renewable resources are not a long-term energy solution. Renewable energy usage is on the rise as coal usage dwindles[3]. However, it’s still a small percentage of the overall picture. The lower the non-renewable energy percentage of total energy use, the lower total emissions will be.
The relationship between these three KPIs for energy & emissions is clear. Companies should strive for lower greenhouse gas emissions. The best way to do that is to use less energy and to use less non-renewable energy.
Water Footprint
The third type of KPIs we will focus on is water footprint – in this section, we will explore the two key KPIs to consider when measuring a supply chain’s overall water footprint. These two KPIs are the percentage of water reused / recycled and the total water discharged by quality and location.
Percentage of Water Recycled & Reused – Increasing recycled and reused water percentages can lead to reduced costs, and potentially tax-credits[4]. This aligns with many OEMs’ goals to make zero water withdrawals for manufacturing processes.
Total Water Discharged by Quality and Location – Water-based ecosystems can be delicate in nature. Damaging them could have negative long-term effects on your local area and business prospects. Organizations that fail to include this metric in their water footprint calculations, fail to measure the entire impact their manufacturing processes may have on water.
Reclamation
The fourth type of KPIs we will focus on is reclamation – here, we will explore two categories: reclaimed material percentage and the rate of biodegradable materials.
Reclaimed Material Percentage – The higher the percentage of material used in production that either is reclaimed, or can be reclaimed, the more sustainable the organization is, as a whole. This metric coupled with the raw material weight in the Raw Materials section does a good job quantifying the impact on the resources used, for both new and reclaimed. As stated in our first post in this series, this aligns with many OEMs’ goals to reach true zero waste to landfill.
Biodegradable Materials Rate – Biodegradable materials, especially in packaging, can have a tremendous impact on decreasing the waste that is generated[5]. OEM aftersales can differentiate themselves by leading the field towards sustainability through use of biodegradable materials. This could also have a positive brand image impact due to the cultural push towards sustainability in younger generations of buyers.
Human Cost
The last type of core KPIs is human cost – we will explore the metrics to consider when organizations want to measure the total impact their manufacturing processes have on people. Specifically, we will look at the portion of the population exposed to negative health outcomes and the usefulness of the product lifetime.
Portion of the Population Exposed to Negative Health Outcomes – Negative health outcomes are wide-ranging. For example, noise pollution has been linked with hearing loss in staff of loud facilities, which could lower productivity in the workforce[6]. Air pollution is included here as well – beyond greenhouse gas emissions, air quality issues have detrimental health outcomes for people in affected areas. There are also many other possible negative health outcomes, including mine tailings leaching into water supplies and toxic chemicals used in the manufacturing process that impact worker health, among others.
Biodegradable Materials Rate – All else equal, a longer useful product lifetime leads to lower emissions per end user. New regulations such as the European Union’s Eco-Design directive require reduced energy consumption and emissions throughout the production lifecycle of a product[7]. Longer useful product lifetime can help an organization gain competitive advantage on the axis of quality.
In Our Next Post…
We’ve shared our perspectives and insights into the core metrics organizations can use and consider when measuring how their manufacturing processes impact the environment. We did this exploring the different inputs that impact the five key drivers of sustainability – Raw Materials, Energy & Emissions, Water Footprint, Reclamation, and Human Cost. In the next segment of this four-part series, we will dig even deeper to understand the framework organizations can use to truly measure their impact on the environment and how mediation methods impact the profitability of their businesses. This framework will help aftersales supply chains balance sustainability with cost.
[1] https://www.epa.gov/ghgemissions/sources-greenhouse-gas-emissions
[2] https://www.osti.gov/pages/servlets/purl/1342660
[3] https://www.eia.gov/energyexplained/use-of-energy/industry.php
[4] https://www.corporatevision-news.com/6-ways-water-efficiency-can-save-your-business-money/
[5] https://www.ncbi.nlm.nih.gov/pmc/articles/PMC2873018/
[6] https://www.ncbi.nlm.nih.gov/pmc/articles/PMC5348948/
[7] https://www.eceee.org/ecodesign/process/
Authors
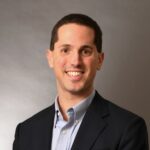
Nate Chenenko
Director